About Defect Sorting Service (DSS)
Defect Sorting service is performed on the FAILED inspection to segregate as many products as possible with known or identified defects (example: appearance, functionality, safety, workmanship, color etc.) in a Shipment.
Other checks will not be done during this inspection. The defect sorting service is done with maximum sample size or 100% by focusing on one or few specific defects by not focusing other defects that are acceptable in small numbers.
Benefit of doing DSS is the specific defect which is reworked is the focus of inspection and hence, customer can confirm whether to take the products or to drop it with the result that shows the percentage of defects affecting your products.
Importance of DSS:
- Transparency in the percentage of known or identified defects affecting your product.
- To ensure factory has reworked on critical issues after a failed inspection
- Give customers a clear picture of the quality of products to decide about shipment
- Protects the brand reputation by avoiding inferior quality products sent to market
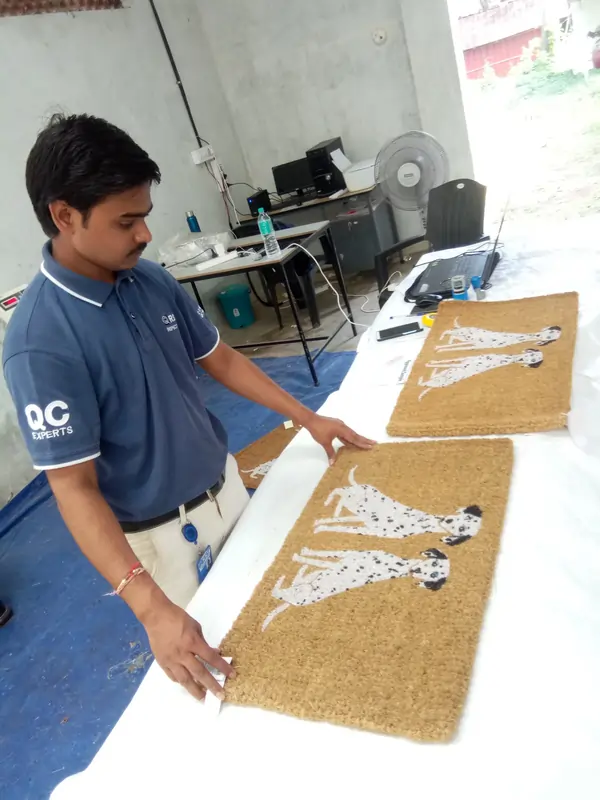